Hot Induction Bending Process
Induction bending (also known as "hot bending" and sometimes as "hot rolling") happens when heat is applied to a specific area of a metal tube or steel pipe. It is usually with the use of an induction coil to make the material easier to bend to a preset radius. The bending process start when place the straight steel pipe in the machine bed with an induction heating coil located around the pipe at one end. This heating coil creates a narrow, circumferential, heated band around the material. As the steel is heated to between 800 and 2,200 degrees Fahrenheit, it is slowly pushed forward through the coil at a consistent speed and temperature and shaped into a bend. After the material passes through the coil, the steel pipe is quenched by a controlled water cooling system.

Hot Induction Bend Manufacturing Process
Hot Induction Bend Manufacturing Specification
Induction Bending is a controlled means of bending pipes through the application of local heating using high frequency induced electrical power. As a leading manufacturer of induction bends, PRIME STEEL PIPE produce the most demanding bends for the nuclear, chemical, petrochemical and energy sectors as well as onshore and offshore oil and gas pipeline systems. Our bending materials including carbon steel, stainless steel and alloy steel with the pipe type of seamless steel pipe, erw steel pipe, lsaw steel pipe, spiral welded pipe. The bending dimensions ranges from NPS 1/2'' to 72'' with the wall thickness up to 120mm. The bending angle is from 15 degree to 180 degree, and the bending radius is ranging from 2.5D to 10D.

Seamless Hot Induction Bend Specification Sheet
ERW Hot Induction Bend Specification Sheet
LSAW Hot Induction Bend Specification Sheet
SSAW Hot Induction Bend Specification Sheet
Hot Induction Bend Manufacturing Standard
API 5L: Specification for Line Pipe
ASME B16.49: Factory Made Wrought Steel Butt-welding Induction Bends for Transportation and Distribution Systems
ASTM A234: Standard Specification for Piping Fittings of Wrought Carbon Steel and Alloy Steel for Moderate and High Temperature Service
ASTM A312: Standard Specification for Seamless Ferritic and Austenitic Alloy Steel Boiler, Superheater, and Heat-Exchanger Tubes
ASTM A403: Standard Specification for Wrought Austenitic Stainless Steel Piping Fittings
API 5L Pipe Bend Technical Data
ASME B16.49 Pipe Bend Technical Data
ASTM A234 Pipe Bend Technical Data
ASTM A312 Pipe Bend Technical Data
ASTM A403 Pipe Bend Technical Data
Hot Induction Bend Coating
Along with build quality, the longevity and reliability of hot induction bend is highly dependent on the type and quality of the coating used. However, applying coatings to pipe bend is not just about preventing corrosion, but can affect the evenness of flow through the pipe and the need to prevent contamination of pipe contents ((e.g. foodstuffs or drinking water). PRIME STEEL PIPE offer corrosion resistance coating service for hot induction bend, our coating service includes light oiling, black painting, FBE coating, 2 layers or 3 layers PE coating, hot dip galvanizing.
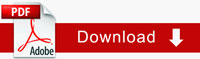
FBE Coating for Steel Pipe Elbow
2PE/3PE Coating for Steel Pipe Elbow
Hot Dip Galvanizing for Steel Pipe Elbow
Hot Induction Bend Pakcing Requirements
We focus on every procedure to assure quality, the package we usually take is pack the steel pipe elbows with environmental poly bags, and then in free fumigation wooden cases or wooden palte. We also accept customized package such as OEM by negotiation.
1. Material shall be packed ready for export in a manner which allows easy handling and prevents damage. Vendor shall submit their standard packing procedure to purchaser for approval.
2. Open ends of fittings and flanges shall be supplied with heavy duty plastic protective plugs or caps. For bevelled ends, the caps shall protect the full area of the bevel.
3. Water proof barrier material shall be used for stainless steel materials to protect against chlorine attack by exposure to salt water atmosphere.
4. Carbon steel and stainless steel items are not allowed to be stored together and shall be packed separately.
The Advantages of Hot Induction Bending
1. The ability to heat a specific area of the steel pipe will ensure a minimal amount of distortion occurs after the bend is completed. 2. Induction bending results in higher energy efficient systems since the power required to create the bend is kept to a minimum. 3. With the induction bending process, sand filling and internal mandrels are not required. 4. Bending times do not take as long as other processes, making induction bending more cost effective. 5. And finally induction bending eliminates the need for mechanical or welded joints, resulting in a smoother finish. 6. This hot bending process is a preferred alternative to the traditional cold bending process as it limits wall thinning, rippling and ovality. 7. It is the consistency and predictability of this bending process that contributes to the high quality and reliabity of bends. 8. Heat induction bending enables the bending of large pipes, steel beams, as well as square and rectangular tubes.